solution
A car part manufacturing company currently produce a suspension assembly for Toyota Motor Corporation. Figure 1 shows the breakdown structure of the suspension assembly and Figure 2 shows the final assembly and how to fit into a car. Table 1 shows the name of components, part numbers and number of components in each suspension assembly.
Table 1: Parts list for Suspension Assembly
Number in Figure 1 |
Part number |
Part name |
Amount per assembly |
1 |
PA-T15-001 |
Shock absorber unit |
1 |
2 |
PA-T15-002 |
Lower insulator |
1 |
3 |
PA-T15-003 |
Spring bumper |
1 |
4 |
PA-T15-004 |
Coil spring |
1 |
5 |
PA-T15-005 |
Upper insulator |
1 |
6 |
PA-T15-006 |
Spring upper seat |
1 |
7 |
PA-T15-007 |
Bushing |
1 |
8 |
PA-T15-008 |
Suspension Support |
1 |
9 |
PA-T15-009 |
Washer |
1 |
10 |
PA-T15-010 |
Stop nut |
1 |
11 |
GE-001 |
Bolt |
2 |
12 |
GE-002 |
Nut |
5 |
As you can notice from the part number, all parts except bolts and nuts are special purpose parts only necessary for this specific suspension assembly. All parts are purchased from outside benders except the coil spring. Note that sampling inspection is conducted for all purchased parts before they are used for the final assembly.
Coil springs are produced in-house. The process to produce the coil spring in the company is as follows.
- a) Heating the wire: to an appropriate temperature for the winding process.
- b) Hot winding process: with a spring winding machine to align the wire into a proper pitch.
- c) Cutting the wire: cut the wire in an appropriate length after the winding process.
- d) Cooling process: cool down the spring immediately by plunging into oil.
- e) Heat treatment: remove internal stress within the material to provide higher resilience. Usually heated in an oven and held at an appropriate temperature for a predetermined time.
- f) Grinding: the spring needs to have flat ends. The coiled spring will be placed into a jig by operators to feed into the grinding machine.
- g) Shot peening: this process requires strengthening the steel to resist fatigue and cracking during its lifetime.
- h) Coating: to prevent corrosion, the entire spring surface will be coated by dipping into a liquid rubber.
- i) Inspection and Transporting: the final coil spring will be inspected and transported to the final assembly workstation.
Using the info above, answer the followings
Q1.The number of workers and the number of parts produced in each process are assumed to be as shown in Table 2. Using this data, find the productivity in the following.
Table 2: Process for coil spring production
Process |
No. of employees |
The number of parts produced in each process per hour |
Heating /hot winding/cutting the wire |
4 |
80 |
Cooling process |
4 |
110 |
Heat treatment |
5 |
160 |
grinding |
5 |
80 |
Shot peening |
5 |
100 |
Coating |
4 |
80 |
Final inspection and transportation of coil spring |
9 |
80 |
- The final assembly of the suspension will be done at the end of the process before it is dispatched to another workstation. The final assembly requires 10 workers and can make 80 final assemblies per hour.
- Assume that the inspection workers shown in Table 2 are also involved in the sampling inspection for all parts listed in Table 1.
- Input for the productivity calculation:
- Normal pay rate for inspection/transportation workers is $65/hour and all other workers including the final assembly are paid at $50/hour.
- The workers are normally working 8 hours per day and 5 days per week.
- The overhead cost for each worker is $300 per week.
- The material cost for each coiled spring is $70.00 and assume 7 coil springs process listed in Table 2 will take the equal amount of material cost.
- All other material cost for suspension final assembly (all parts listed in Table 1 except the coil spring) is $185.00.
- Output of the productivity calculation:
- Assume that the company can sell all produced final assemblies of suspension at $650.00 each.
- For the output calculation, assume that 70% of the selling price could be distributed towards the coil spring production process and the remaining 30% is for final assembly process.
- Also assume that 7 coil springs process listed in Table 2 will take the equal amount of selling price as the output of each process, i.e., the output of each process will be 10% of selling price of final assembly.
A) Find productivity in both labour productivity and total productivity of each process listed in Table 1?2and the final assembly.
B) The operation manager is now considering the following three different options to improve the current productivity. Find productivity in both, labour productivity and total productivity for the three options for each process listed in Table 1?2and the final assembly. Which option is the best in terms of the total productivity improvement?
i) Increase the production across all processes including the final assembly by 20%. All other conditions (including costs) are the same
ii) Increase the final assembly selling price 15%. All others are the same
iii) Reduce the labour cost across all processes including the final assembly by 10% with some cost saving measure. Note this is not the reduction of workers. This is simply the reduction of labour cost by 10%. Overhead cost is also reduced by 10%.
"Looking for a Similar Assignment? Get Expert Help at an Amazing Discount!"
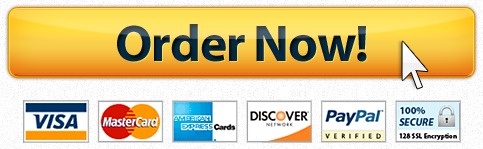